1. Raw Material Preparation
- Cathode Material Preparation: The cathode is typically made from lithium compounds such as Nickel-Cobalt-Manganese (NCM) or Nickel-Cobalt-Aluminum (NCA). These materials are mixed with conductive agents and binders to form a slurry.
- Anode Material Preparation: The anode is usually made from graphite or silicon-based materials, mixed with conductive agents and binders, and also formed into a slurry.
- Electrolyte Preparation: The electrolyte is a lithium salt (like LiPF6) dissolved in organic solvents, facilitating the movement of lithium ions between the electrodes.
2. Electrode Coating
- Coating Cathode and Anode: The cathode and anode slurries are evenly coated onto current collectors (aluminum foil for the cathode, copper foil for the anode).
- Drying: The coated electrodes are dried in high-temperature ovens to remove any residual solvents, ensuring a uniform and solid electrode layer.
3. Roll Pressing
- After coating, the electrode materials are pressed using rolling machines to increase electrode density, which boosts energy density and ensures consistency.
4. Electrode Cutting
- Electrode Sheet Cutting: The dried and pressed electrode sheets are cut into appropriate sizes, depending on the battery design (pouch, cylindrical, or prismatic cells).
5. Cell Assembly
- Winding or Stacking: The electrodes, along with a separator (which prevents direct contact between the cathode and anode), are either wound into cylindrical shapes or stacked into layers for prismatic or pouch cells.
- Electrolyte Filling: Electrolyte is injected into the assembled cells, allowing for the movement of lithium ions between electrodes.
- Sealing: The cell is sealed to prevent moisture or air from entering. Sealing can involve aluminum-plastic laminate (for pouch cells) or metal casing (for cylindrical or prismatic cells).
6. Formation and Aging
- Formation: The cell undergoes an initial charge and discharge cycle, known as formation. This process allows a protective Solid Electrolyte Interface (SEI) to form on the electrode surfaces, stabilizing the battery chemistry.
- Aging: After formation, the cells are stored (aged) at specific temperatures to stabilize internal reactions, ensuring consistent performance.
7. Battery Pack Assembly
- Cell Testing: After formation and aging, each cell undergoes rigorous testing, including capacity, internal resistance, and safety evaluations.
- Battery Module Assembly: Cells are combined into modules, which are connected in series or parallel configurations. A Battery Management System (BMS) is integrated to monitor performance and safety.
- Module Packaging: The modules are then packaged into the battery enclosure, with additional components like cooling systems and protective circuits.
8. Quality Control
- Final Testing: After assembly, the battery packs undergo a final round of tests, including charge-discharge performance, temperature behavior, mechanical strength, and safety testing.
- Packaging and Shipping: Once passing all quality checks, the battery packs are packaged and prepared for shipment.
9. Waste Recycling
- During production, materials such as excess electrode coatings or residual electrolyte are collected for recycling to minimize waste and environmental impact.
Key Process Controls:
- Clean Environment: Many stages, particularly electrode coating and cell assembly, require a dust-free, moisture-controlled environment, as impurities can degrade battery performance.
- Electrolyte Handling: Electrolytes are sensitive to moisture, and improper handling can negatively impact battery life and safety.
This structured process ensures high performance, safety, and efficiency in lithium-ion battery manufacturing.
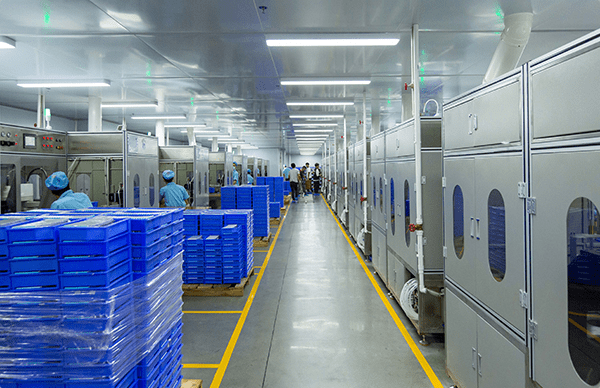
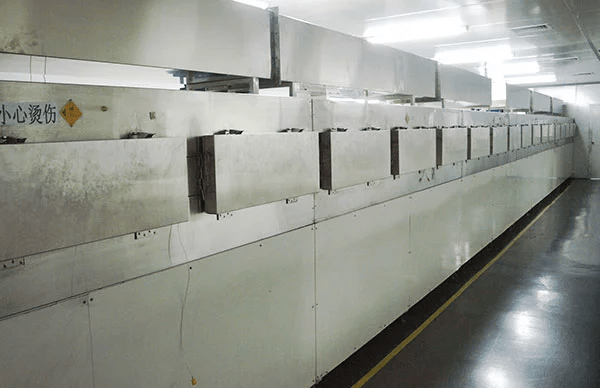
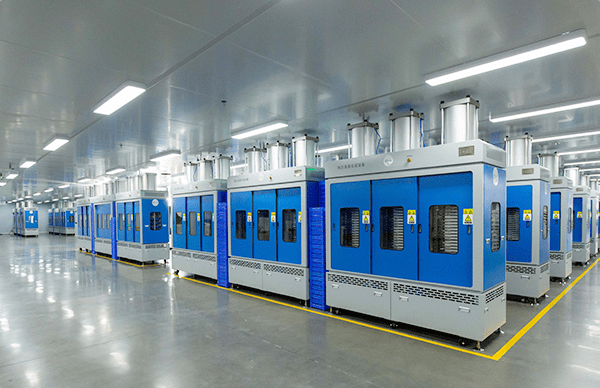